Partnering with Li Industries: Pathway for Direct Lithium-Ion Battery Recycling
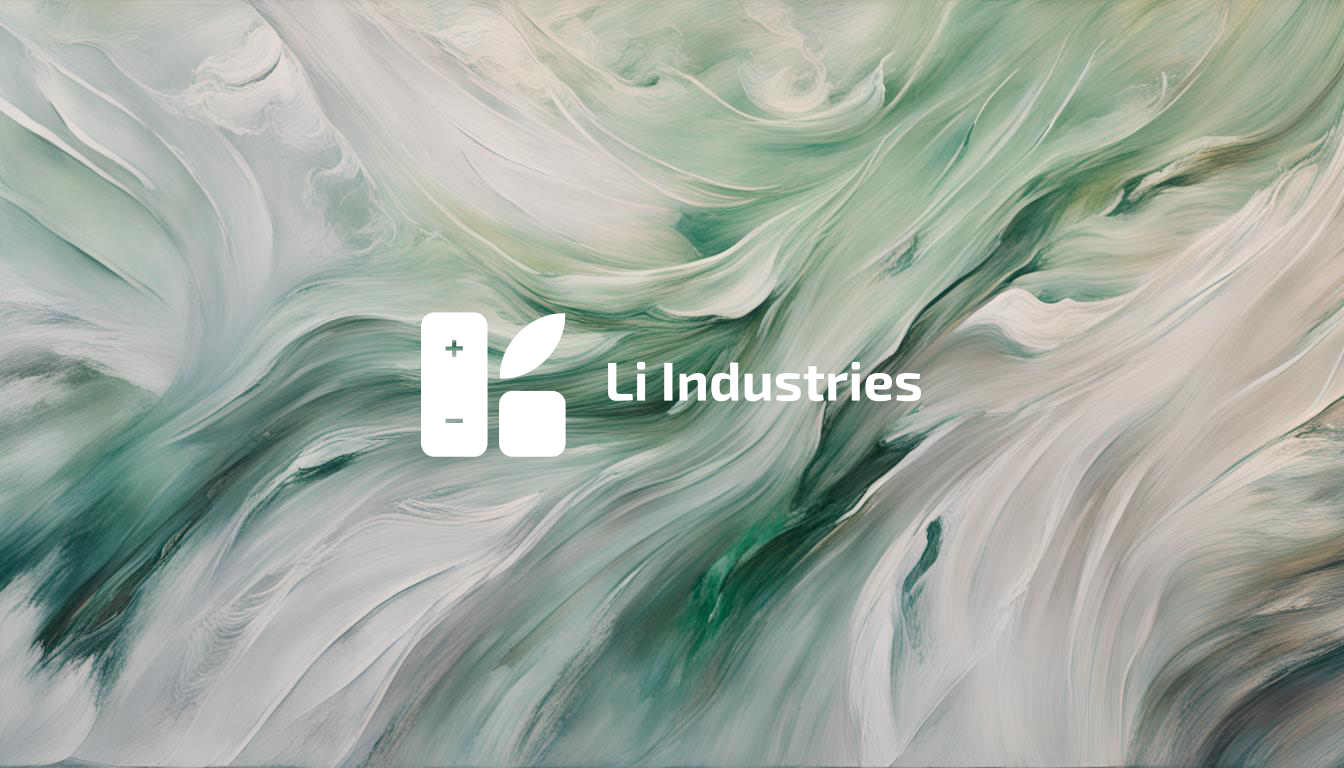
In 2019, the Nobel Prize in Chemistry was awarded to Stanley Whittingham, John Goodenough, and Akira Yoshino in recognition of their groundbreaking, foundational work on lithium-ion batteries. Their efforts served as a watershed moment for the electrification of the world. By enabling long-duration, wireless power, they have enabled true energy transformation across a range of markets.
Nowhere is this more evident than in the context of electric vehicles (EVs). Lithium-ion batteries have powered a revolution in EV innovation and development with performance in some cases now exceeding traditional internal combustion engines — including a 50% improvement in energy efficiency, lower maintenance and operating costs, and optimized application of torque [1]. Companies like Tesla have pushed the ranges of their EVs to over 400 miles in some cases, with over 1000 horsepower, and a 0–60mph acceleration times of less than 2 seconds [2]. Given the pervasive and enabling nature of the technology, lithium-ion demand and production have naturally seen a meteoric rise over the past 10 years (0.5 to 526 GW-hr by 2020) with an expected demand of over 9300 GW-hr by 2030 — pictured in Figure 1 [3–4]. In terms of adoption rate, EVs as a whole are expected to see up to a seven times increase in production, and by 2030 are projected to encompass more than half of the total vehicle market share [5].
This increasing demand represents its own strategic and logistical challenge in terms of the availability of materials from which to produce each battery. From a materials standpoint, lithium-ion batteries consist of four main components [6].
- A positively charged cathode from which lithium-ions originate(usually some lithium-metal-oxide compound);
- A negatively charged anode material (usually graphite or copper),which receives lithium ions;
- An electrolyte medium that both cathode and anode are immersed in, which allows the flow of lithium ions between the cathode to the anode, and;
- A separator or separation membrane, which ensures the two are not in contact with each other.
While producing each of these four components is not trivial, a more fundamental challenge is the rarity and distribution of the elements needed to make them tick — i.e. cobalt, nickel, and of course lithium.
The largest concentrations of raw lithium are spread across only a few key regions of the world, with over 56% of the global supply located in Argentina, Bolivia, and Chile, with the remainder unevenly spread out globally [7], with some small reserves in Australia, the United States, and China. Cobalt and nickel are just as, if not more, difficult to extract and have even more limited availability. Cobalt is almost exclusively found in meaningful quantity in the Democratic Republic of the Congo, with serious concerns associated with the use force and/or child labor [8]. Because of the combined strains of limited supply, mixed with uneven global distribution of resources, the supply chain for batteries is inherently linked to geopolitical issues and other external environmental and societal stressors.
Up to the current day, such strategic issues have been surmountable as production has remained on a relatively small scale. However, with the exponentially increasing demand and projected demand for Li-ion batteries in the near future, the industry must contend with how to ensure the continued viability of the technology in spite of near-term and long-term availability challenges. Thankfully, lithium battery materials, unlike hydrocarbon fuel-driven processes, allow for the (at least partial) circular reuse of non-renewable resources. In short, we can recycle them! Instead of the need to mine, refine, and produce each new battery from virgin raw material, valuable components and materials can be extracted from used batteries at various stages of life and repurposed for new units.
Not only can circularity in the battery materials’ value chain provide a crucial supply of resources in response to limited availability, but battery recycling can also improve the efficiency of standard production. Currently, 5–10% of cathode material (specifically) throughout the manufacturing process is scrap, which is immediately ready for reuse [9]. Considering that a typical EV battery will be in circulation for approximately 10 years before end-of-life, a significant majority of near-term battery recycling opportunities align with the massive scaling of global battery production. In time, as EV batteries reach end of life, the amount of batteries to be recycled will be truly astounding. However, how recycling and reuse are executed can vary greatly.
Technology Landscape: Where We Are & Where We’re Headed
The technical landscape of battery recycling is best understood in comparison to the standard lifecycle of a battery. Described in terms of value chain, the life of a battery starts with the mining of the key resources, followed by the refining of those resources into a usable state, followed by component production, battery unit manufacturing, and finally, battery use. After use, more often than not, the standard practice is for the batteries to go to a landfill, or sometimes sent for second (albeit degraded) use in applications like residential energy storage. Battery recycling processes are working to turn this linear value chain into a cycle. Figure 2 illustrates the initial first-use value chain (along the bottom), and then overlays potential interjection points for recycled materials depending on methodology [10].
Using Figure 2 as a guide, the first pathway to circular reuse of lithium-ion battery materials is the oldest and most well-known process, albeit the most inefficient — pyrolysis (pyro) processing. As the name implies, this method of recycling burns down the used battery to its raw base material elements. Simple and straightforward, this process exists at scale today. However, the process is inherently dirty, energy-intensive, and costly, providing the lowest yield rates due to material loss.
In answer to the low-yield inefficiencies of pyro, existing technologies used for electronic materials waste recycling have been adapted for use in batteries. These hydrometallurgical (hydro) processes are becoming a rapidly scaling alternative to pyro and leverage sulfuric acids and other corrosive fluids to dissolve specific aspects of used battery units isolating recoverable components (such as the cathode) [11]. By doing so, more of the overall battery materials can be reused and leveraged. The catch? The processes themselves are lengthy and time-consuming (and therefore costly), requiring the use of dangerous pollutive chemicals for operation. The acids are incredibly destructive, and as a result, some potentially reusable components are still lost, along with the generation of significant waste products including contaminated wastewater. While such cons are notable, this process is an effective way of isolating cathode components, which can then be routed back into the cathode production stage of life-use.
The third circular pathway is direct recycling, which draws the shortest path possible between waste and new production. Direct recycling avoids breaking down battery components to their most basic constituent elements, which would subsequently require reconstitution into components for re- introduction into a battery manufacturing process. By recovering, preserving, and rejuvenating critical battery components — such as cathode materials — in whole, recycled battery components are ready for re- insertion into the manufacturing process directly from the recycler. In the case of recycling manufacturing scrap, opportunities to co-locate direct recycling processes enable complete circularity of production scrap on-site.
As alluded to earlier, each of these three approaches has its own unique pros and cons. The current state of the art is typically hydro, with pyro being well known but avoided in many jurisdictions given how environmentally toxic the process is. In both cases, the recyclers must then have either close ties with or have captive electrode production expertise and capabilities to ensure product off take. For these reasons, direct recycling has significant appeal to the industry given the implications on a simplified and economical circular supply chain. It has already been demonstrated that direct recycling processes can produce materials of quality near that of virgin products. The key technical challenge is scalability. Pyro and hydro are both “mature” technologies with a decade or more of development behind them. Direct recycling technology is much newer, has yet to scale, and is just now starting to be adopted by the market. But with the projected growth of lithium battery demand, the future is bright for innovations that deliver scalable and optimal solutions for circularizing the battery manufacturing supply chain.
Market Outlook: What Technology is Needed & Vision for the Future
The continued rise of lithium-ion batteries and the growing need to secure critical materials for their production undergirds the importance of direct recycling technologies. A direct recycling company would be servicing a $9.2 billion total addressable market by 2030, and that’s if the only focus was on manufacturing scrap alone — excluding end-of-life battery feedstock, which will grow rapidly as EVs begin to retire following an average 10-year life cycle. Figure 3 reviews available material projections.
A key driver of recycling is lithium-ion battery cost. As referenced in Figure 1, the cost of lithium batteries has dropped significantly over the past decade. However learning curves and economies of scale have recently been overcome by the rising cost of raw material inputs for battery production, as evidenced in the cost of lithium batteries actually rising in 2022 as lithium battery demands exceed component supply. Cathode materials and production make up about 50% of the overall battery cost. Different battery chemistries (i.e. cathode chemistries) contain different amounts of specific materials, or in some cases different materials altogether. In terms of rarity and supply, the materials of most concern (highest value) are the previously mentioned cobalt, nickel, and lithium. The economics of respective recycling methods (pyro, hydro, etc.), as well as their inherent limitations, vary greatly when considering these fundamental constituent elements. For example, expensive processes like hydro make the recycling of lower-value components intractable from a cost standpoint. Nickel and cobalt-rich chemistries, which have a high price point can warrant the resource usage required by hydro, but others — like lithium iron phosphate, lithium iron phosphate batteries (LFP), which has no cobalt or nickel — do not. As lower- cost typologies like LFP become more prevalent, and indeed the only viable options to cope with resource scarcity, other lower-cost recycling methodologies will be required to viably recycle and still retain a price point less than that of a first-use battery.
Direct recycling is an important innovation that directly responds to these challenges by enabling the recycling of a robust range of chemistries, including those without cobalt or nickel. Naturally, the market characteristics are expected to become particularly favorable in the coming years, in inverse correlation with material availability. As previously mentioned, battery production is already on the rise, but a wave of domestic production within the United States and North America is expected — spurred on by incentives in the Inflation Reduction Act, upon which dozens of plants are planned to be built over the next few years. We can expect the future of battery production to be more regional and distributed across major EV markets compared to being largely concentrated in China today, and a corresponding demand for regionally secure supply of critical battery materials, which direct recycling will help enable.
To properly address the market as a whole, however, key innovations must be applied to direct recycling to meet industry demand and to be capable of scale of tractable relevance.
Investing in “A New Age of Battery Recycling”
In reviewing innovators in the battery recycling space, Li Industries quickly distinguished themselves as game changers in the realm of direct recycling lithium-ion batteries. With their team, led by world class experts stemming from MIT, Virginia Tech, and Wharton, along with advisement by Nobel Laureate and father of lithium-ion batteries Stanley Wittingham, the company has holistically redesigned the battery recycling process.
Using its proprietary method, Li Industries separates each battery into its respective electrode components — anode and cathode, which can then be immediately reintroduced into the battery manufacturing process. A step further, upon sorting and recovering the electrode materials, the process purifies and rejuvenates active compounds. Validated and tested directly by battery manufacturers in an industrial setting, Li Industries has demonstrated its recycled battery performs equivalently to virgin manufactured units [12].
Firmly categorized as direct recycling, its process doesn’t require any of the high energy costs of pyro processing or the time intensive and toxic procedures required by hydrometallurgy. Li Industries has designed its systems to ensure high speed, low cost, and scalability — and thus filling the critical niche identified in the market background. The technique is also environmentally friendly, unlike alternatives.
Li Industries is also uniquely capable of economically recycling lithium iron phosphate batteries, which comes at a critical time as the chemistry rapidly gains traction across the industry. The economics of standard recycling processes (hydro and pyro) are such that the economics are not viable when lower-value elements are considered. Li Industries low-cost process can be much more competitive on the margins with a more robust range of chemistries including LFP as well as those which contain nickel and/or cobalt (LCO, NMC, etc) [12].
Strategic Alignment: Why We Invested
Based on our technology landscape analysis and understanding of the market overall, Li Industries has distinguished itself as a category leading company in the direct recycling of li-ion batteries. By enabling scalable, low- cost recycling of batteries with the equivalent performance of virgin units, they provide a solution to several battery material supply challenges and serve as an enabler of circularity and electrification in mobility — both of which are investment focus areas aligned with Xerox Ventures’ Green Enterprise thesis.
Xerox Ventures invests in the future of business solutions across all industries, and Li Industries is pioneering the frontier of a fully circular and regionally secure supply chain of critical battery materials. The innovations the company is commercializing will provide sustainability and resiliency to a segment currently exposed to significant geopolitical and supply chain risks. Further, Li Industries is uniquely able to bring circularity to a rapidly growing class of battery chemistries that does away with the challenges and cost of sourcing nickel and cobalt.
References
[1] ICE vehicles vs. electric vehicles. (2022). Elastoproxy. https://www.elastoproxy.com/ice-vehicles-vs-electric-vehicles/
[2] Model S. (n.d.). Tesla. https://www.tesla.com/models
[3] Bloomberg. (n.d.). Bloomberg — Are you a robot?. https://www.bloomberg.com/news/articles/2020-12-17/this-is-the-dawning- of-the-age-of-the-battery?srnd=green
[4] Lithium-ion battery costs decline as manufacturing capacity expands. (2021, September 29). Freeing Energy. https://www.freeingenergy.com/facts/learning-lithium-ion-batteries- economies-price-decline-g202/
[5] Lewis, M. (2022, June 1). This is where electric vehicle adoption is headed between 2022 and 2025. Electrek. https://electrek.co/2022/05/31/this-is- where-electric-vehicle-adoption-is-headed-between-now-and-2025/
[6] The four components of a Li-ion battery. (n.d.). Samsung Li-Ion Battery & Renewable Energy | Samsung SDI Official Site. https://www.samsungsdi.com/column/technology/detail/55272.html
[7] Lithium monopoly in the making? Beijing expands in the lithium triangle. (2022, August 26). Geopolitical Monitor. https://www.geopoliticalmonitor.com/lithium-monopoly-in-the-making- beijing-expands-in-the-lithium-triangle/
[8] The DRC mining industry: Child labor and formalization of small-scale mining. (n.d.). Wilson Center. https://www.wilsoncenter.org/blog-post/drc- mining-industry-child-labor-and-formalization-small-scale-mining
[9] Johnson Matthey partners with onto on direct recycling of Li-ion battery scrap. (2021, September 20). Green Car Congress. https://www.greencarcongress.com/2021/09/20210903-jmonto.html
[10] DOE launches its first lithium-ion battery recycling R&D center: ReCell | Argonne national laboratory. (n.d.). Argonne National LaboratoryArgonne National Laboratory. https://www.anl.gov/article/doe-launches-its-first- lithiumion-battery-recycling-rd-center-recell
[11] Vieceli, N., Casasola, R., Lombardo, G., Ebin, B., & Petranikova, M. (2021). Hydrometallurgical recycling of EV lithium-ion batteries: Effects of incineration on the leaching efficiency of metals using sulfuric acid. Waste Management, 125, 192–203.
[12] Direct Li-ion battery recycling. (2022, August 1). Li Industries | A New Age of Battery Recycling. https://www.li-ind.com/li-industries-direct-li-ion- battery-recycling
Explore our latest investments, news, and insights.
Please try different keywords.